Managing Risks Associated with Manual Handling Tasks
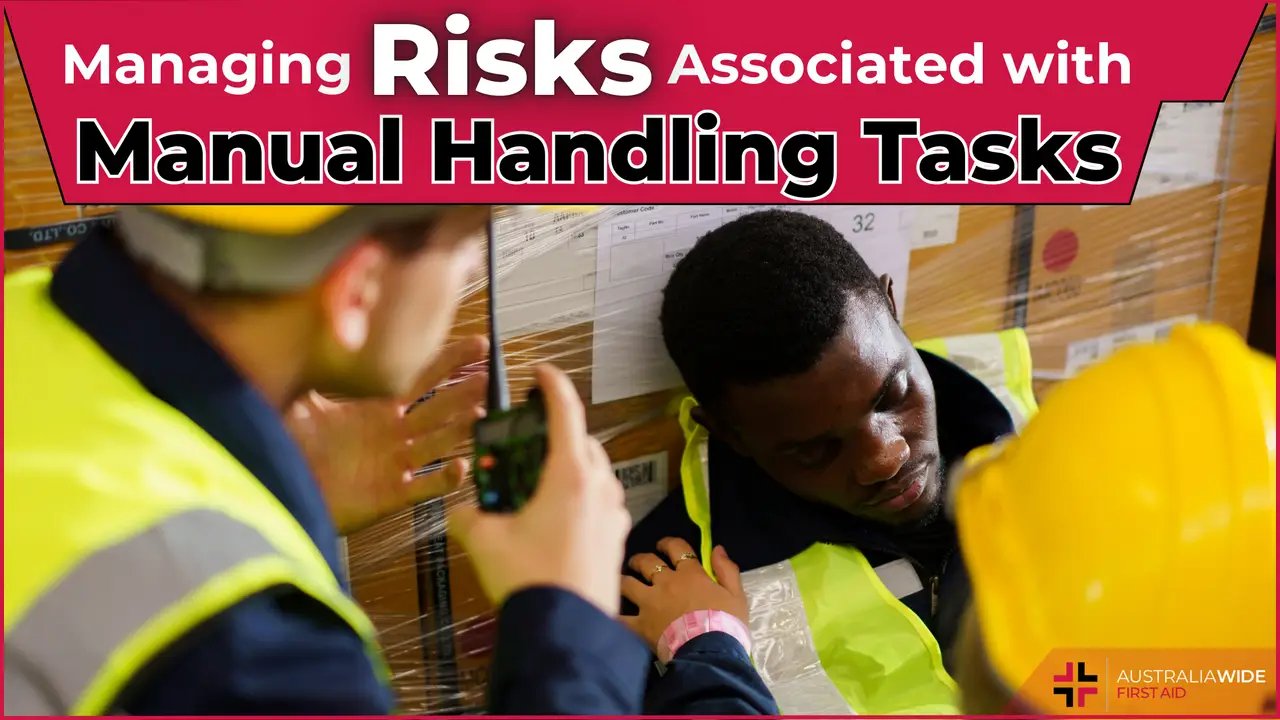
Almost every job involves using the body to carry out some type of manual task.
Some tasks may be hazardous, causing injuries such as musculoskeletal disorders (MSDs).
A hazardous manual task is any activity that requires a person to lift, lower, push, pull, carry, move, hold, or restrain an object, person, or animal that involves one or more of the following risk factors:
The term ‘force’ here describes the amount of muscular effort needed to perform a task or movement. This force can overload joints, discs, tendons, and muscles and are associated with most MSDs.
Hazards can cause varying degrees of harm, from minor discomfort to serious injury. Many hazards and their associated risks are well known and have well-established and accepted control measures. In these situations, a formal risk assessment may not be required if the risk and its controls are already understood and effective controls can be implemented directly.
The risk management process for safe manual handling involves several key steps aimed at identifying, assessing, and controlling risks associated with manual handling tasks. This process ensures the safety and health of workers by minimizing the potential for injuries.
The steps include:
By following this risk management process, organizations can significantly reduce the risk of injuries related to manual handling, ensuring a safer and healthier workplace.
Identifying all hazardous manual tasks is the first step in the risk management process. This involves finding all relevant factors and situations that may contribute to MSDs.
Hazards generally arise from the following aspects of work and their interaction:
Hazards may be identified by examining the workplace and how work is carried out. A manual task is hazardous if it involves any of the following characteristics:
Workers who perform manual tasks can provide valuable information about any discomfort or muscular aches and pains they experience while performing particular tasks, which can signal potential hazards.
Reviewing records of workplace injuries and incidents, inspection reports, sick leave, worker complaints, and any workers' compensation claims made for an MSD can help identify which manual tasks may cause harm. However, not all hazardous manual tasks will be associated with reported incidents, so it is important to gather additional information.
A risk assessment involves evaluating what could happen if someone is exposed to a hazard and the likelihood of it occurring. For hazardous manual tasks, this means examining the hazards associated with the task to assess the likelihood of the forces, movements, and postures giving rise to a musculoskeletal disorder (MSD).
You should carry out a risk assessment, in consultation with workers, for any manual tasks identified as hazardous unless the risk is well known and you already know how to control it.
To make use of a risk matrix such as this, first determine how serious an injury resulting from the task would be. For example, would it require a band-aid, or would it lead to permanent disability or death?
Then determine the likelihood of an injury occurring. Make this determination by excluding any assistance, equipment, or correct techniques. For example if a worker were to try to lift a 50kg load on their own, the likelihood of an injury occurring would be ‘Almost certain’.
Once you have determined the level of consequence and the likelihood of an injury occurring, you will see the level of risk associated with that task.
The level of risk determines how to proceed with managing that task:
How to Do a Risk Assessment for Hazardous Manual Tasks
The first step in completing a risk assessment is to identify who should participate in the assessment, such as the workers who do the task, their health and safety representative, and management who control how the task is done.
Note which body parts are likely to be at risk of injury and work through the assessment together to determine which risk factors pose a risk and why. It may help to look at the task in stages to identify all risk factors. Determine which things should be changed to control the risks. For complex situations, expert or specialist advice may be useful.
A task involves a risk of an MSD developing if you answer 'yes' to any of the following:
Question 1: Does the Task Involve Any of the Following?
As a general guideline:
The risk increases as the degree of bending and twisting increases. The risk is greatest when postures and movements are extreme and uncomfortable for the worker. The risk also increases with the magnitude of force, frequency of actions, and speed of actions. The longer a task is performed, the more hazardous it is likely to be.
As a general guideline, a task is performed for a ‘long duration’ if it is done for more than 2 hours over a whole shift or continuously for more than 30 minutes at a time.
Question 2: Does the Task Involve High or Sudden Force?
High or sudden forces can cause an MSD even if they are not repetitive or sustained. Tasks involving high force may be a risk, even if done occasionally or for short periods. The longer and more often force is applied and the higher the force, the greater the risk.
Question 3: Does the Task Involve Exposure to Vibration?
Prolonged exposure to vibration increases the risk of an MSD and other health problems. The risk increases with the duration and amplitude of vibration.
Examples of sources of vibration include:
What are the Sources of Risk?
When conducting a risk assessment, it's essential to identify the sources of any risks present in the task. These sources are elements you may be able to change to eliminate or reduce the likelihood of an MSD.
Common sources of risk include:
Identifying and understanding these sources of risk are crucial for implementing effective control measures to prevent MSDs in the workplace.
The WHS Regulation mandates working through the hierarchy of control measures when managing risks from hazardous manual tasks. The hierarchy ranks control measures from the highest to the lowest level of protection and reliability.
Elimination
Eliminating risks is the most effective control measure and should be the first aim. This can be achieved by:
If elimination isn't practicable because it hinders the end product or service, the risk must be minimized as much as possible.
Substitution
Replace the hazard wholly or partly with something safer.
Isolation
Separate the hazard from people.
Engineering Controls
Implement physical changes to the work area, tools, load, environment, method of handling, or work organization.
Administrative Controls
If risk remains, minimize it as much as possible with administrative controls. These controls are less effective because they rely on human behaviour and supervision and should only be used when no other controls are reasonably practicable, as an interim measure, or to supplement higher-level controls. Administrative controls include work methods or policies and procedures, such as lifting procedures.
For example:
Personal Protective Equipment (PPE)
Any remaining risks must be minimized with suitable PPE. PPE is the least effective control measure because it relies on proper use by workers. PPE should be used when other control measures aren't reasonably practicable, as an interim measure, or to supplement higher-level controls.
For example:
The hierarchy of control measures provides a structured approach to managing risks from hazardous manual tasks. By prioritizing elimination and minimizing risks through substitution, isolation, and engineering controls, PCBUs can effectively protect workers from MSDs. Administrative controls and PPE should be used as supplementary measures to address any remaining risks.
Control measures implemented to protect health and safety must be regularly reviewed to ensure they remain effective in controlling risks associated with MSDs from hazardous manual tasks.
Control measures should be reviewed:
Reviews can occur through workplace inspections to assess the design and operation of control measures; through consultation with workers and safety representatives; and through testing and analysis to verify the effectiveness of control measures.
Key Review Questions
If issues are identified during the review:
Need that piece of paper to give to your employer or put on your resume to show that you actually do care about workplace safety and manual handling, and that you have the skills and knowledge to keep everyone safe? Our fully-online Manual Handling course gives you just that. From your desk or the comfort of your own home, gain the knowledge and skills you need to make sure everyone in your workplace gets home safely at the end of each day.
October 1, 2024
Almost every job involves using the body to carry out some type of manual task. Some tasks may be hazardous, causing injuries such as musculoskeletal disorders (MSDs). Knowing how to manage them is a legal responsibility of all workplaces.
January 10, 2024
In Australia, workplace safety is a top priority, and First Aid plays a crucial role in ensuring the well-being of employees. Workplaces are expected to adhere to specific regulations and guidelines outlined by Safe Work Australia. How does your workplace stack up?
November 24, 2023
No matter how experienced you are as an outdoor activity leader, there are some things you should always do to keep your group safe. Nature can be unpredictable, and so it’s best to be prepared.